I. Introduction to Plain Milling for CNC Machining Services Users
In the dynamic world of manufacturing, understanding core machining processes is crucial for anyone seeking high-quality components. If you’re exploring CNC Machining Services, plain milling is a fundamental technique you’ll encounter. But what exactly is it, and why should it matter to you?
Plain milling is a subtractive manufacturing process that uses a multi-point cutting tool (a plain milling cutter) rotating on a horizontal spindle to remove material from a workpiece. Unlike end milling or face milling, which primarily use the end or face of the cutter, plain milling leverages the circumference of the cutter to create flat surfaces, slots, and contours. It’s a cornerstone of modern manufacturing, especially within precision CNC machining, enabling the creation of parts with exceptional accuracy and surface finish.
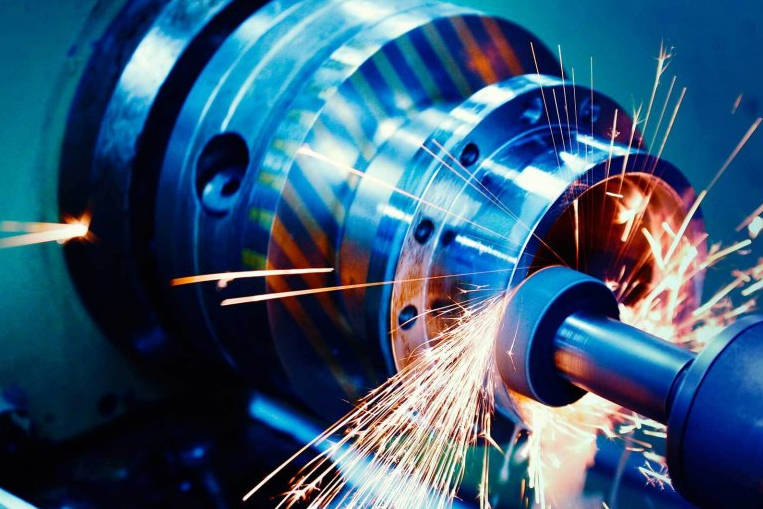
For you, the user of CNC Machining Services, comprehending plain milling empowers informed decision-making. It allows you to:
- Optimize part designs for manufacturability and cost-effectiveness.
- Better understand the capabilities and limitations of your chosen machining partner.
- Ensure that your specifications for flatness, parallelism, and surface finish can be met.
Ultimately, a grasp of plain milling capabilities helps you secure the best possible outcomes for your projects, whether you’re sourcing precision CNC machining parts locally or from a reputable cnc machining china provider.
II. The Plain Milling Process: From Concept to Component
The magic of plain milling lies in its straightforward yet effective mechanics. Imagine a workpiece securely clamped onto a milling machine table. Above it, a plain milling cutter, resembling a cylindrical gear with cutting teeth along its periphery, spins rapidly on a horizontal arbor. As the workpiece is fed into this rotating cutter, the teeth progressively sheer away material, forming chips and revealing the desired shape.
The fundamental mechanics involve a symbiotic relationship between tool rotation and workpiece feed. The rotating cutter provides the cutting action, while the precise movement of the workpiece against the cutter dictates the geometry of the removed material. This controlled removal ensures high accuracy and repeatable results, a hallmark of precision CNC machining.
Key parameters govern this process, directly impacting the quality and efficiency of the machined part:
Parameter | Description | Impact on Process |
Cutting Speed | The speed at which the cutting edge passes over the material (surface feet per minute or meters per minute). | Higher cutting speeds often lead to better surface finishes and shorter machining times, but can also increase tool wear. Crucial for balancing efficiency and tool longevity. |
Feed Rate | The rate at which the workpiece moves into the cutter (inches per minute or millimeters per minute). | Affects material removal rate (MRR) and surface finish. Higher feed rates increase MRR but can degrade surface finish; lower feed rates improve finish but extend machining time. |
Depth of Cut | The amount of material removed in a single pass. | Influences machining time, power consumption, and machine rigidity requirements. Deeper cuts remove more material faster but demand more robust machinery and tooling. |
Tool Material & Geometry | The material (e.g., High-Speed Steel (HSS), Carbide) and design of the cutter. | Dictates tool life, cutting performance, and suitability for different materials. Carbide tools, for instance, are preferred for their hardness and heat resistance in high-speed applications. |
The advent of CNC (Computer Numerical Control) has revolutionized plain milling. Instead of manual operation, CNC systems precisely control every aspect of the machining process – from spindle speed and feed rates to intricate tool paths. This automation ensures unparalleled precision, repeatability, and efficiency, allowing for the consistent production of complex precision CNC machining parts. It minimizes human error, optimizes material utilization, and significantly reduces production times, making cnc machining china a highly competitive global option.
III. Types of Plain Milling Operations and Their Applications
Plain milling isn’t a monolithic process; it encompasses several variations, each with distinct characteristics and ideal applications. The two primary types are conventional (up) milling and climb (down) milling, defined by the relationship between the workpiece feed direction and the cutter’s rotation.
- Conventional (Up) Milling:
- Description: In conventional milling, the workpiece is fed against the direction of the cutter’s rotation. The cutting action begins with a thin chip, which gradually thickens as the tooth advances through the material.
- Characteristics: This method tends to lift the workpiece due to the upward cutting force, often requiring robust clamping. The chips start thin, creating a rubbing action before actual cutting, which can lead to increased tool wear and a rougher surface finish. Backlash in older machines can also be an issue.
- Applications: Primarily used for roughing operations where significant material removal is needed and surface finish is not the primary concern. It’s also suitable for machining work-hardened materials or those with an abrasive scale.
- Climb (Down) Milling:
- Description: In climb milling, the workpiece is fed in the same direction as the cutter’s rotation. The cutter engages the material at its thickest point, and the chip thins out as the tooth exits the material.
- Characteristics: Climb milling offers a superior surface finish and longer tool life compared to conventional milling. The cutting action forces the workpiece down onto the machine table, providing a more stable cut and reducing the tendency for tool chatter. It also reduces cutting forces, making it ideal for thin-walled parts.
- Applications: This is the preferred method for finishing operations where high surface quality and dimensional accuracy are paramount. It’s highly effective for precision CNC machining parts and in situations where maintaining tight tolerances is critical.
Beyond these two main types, specialized plain milling operations leverage the core principle for specific tasks:
- Slab Milling: Utilizes wide plain milling cutters to machine large, flat surfaces quickly and efficiently, often for heavy-duty material removal.
- Straddle Milling: Employs two plain milling cutters on the same arbor to simultaneously machine two parallel surfaces of a workpiece, ensuring high parallelism and productivity.
- Gang Milling: Involves multiple plain milling cutters mounted on a single arbor to perform several operations (e.g., machining different widths or profiles) in one pass, significantly reducing machining time for repetitive tasks.
These variations highlight the adaptability of plain milling, making it a versatile tool in the arsenal of CNC Machining Services providers.
IV. Advantages of Plain Milling for Your Projects
Plain milling offers a compelling set of advantages that make it a go-to choice for countless manufacturing applications, especially when integrated with CNC Machining Services:
- High Material Removal Rate (MRR): Plain milling cutters, particularly those used in slab or gang milling, are designed to remove large volumes of material quickly. This efficiency translates into reduced machining times and lower production costs for parts requiring significant material reduction.
- Excellent Surface Finish (especially with climb milling): As discussed, climb milling consistently produces superior surface finishes, often eliminating the need for subsequent finishing operations. This is crucial for aesthetic components or parts requiring minimal friction and wear.
- Dimensional Accuracy and Precision: When performed on precision CNC machining equipment, plain milling can achieve exceptionally tight dimensional tolerances and maintain excellent parallelism and flatness over large surfaces. This is vital for critical components that must fit perfectly or operate flawlessly.
- Versatility in Materials: Plain milling is adept at machining a vast array of materials, from common metals like aluminum, steel, and cast iron to more challenging materials such as stainless steel, titanium, and various plastics. The choice of cutter material and cutting parameters allows for optimal performance across different material properties.
- Cost-Effectiveness for Certain Geometries: For components requiring flat surfaces, grooves, or slots, plain milling can be highly cost-effective, especially in production runs. The ability to remove large amounts of material quickly and consistently contributes to overall economic viability.
- Scalability for Production: Thanks to CNC automation, plain milling operations can be easily scaled from prototyping and low-volume runs to high-volume production. Once a program is proven, it can be replicated consistently, making cnc machining china a strong contender for large orders of precision CNC machining parts.
V. Real-World Applications Across Industries
The pervasive nature of plain milling is evident in its wide array of applications across virtually every industrial sector that relies on CNC Machining Services:
- Aerospace: From manufacturing structural components like wing spars and fuselage sections to creating mounting brackets and flat panels that demand high strength-to-weight ratios and stringent dimensional accuracy.
- Automotive: Producing critical engine components such as engine blocks, cylinder heads, and transmission cases, where flat mating surfaces and precise oil passages are paramount. It’s also used for machining manifold surfaces and chassis components.
- Heavy Machinery: Creating large, flat surfaces for machine bases, structural members, and industrial fixtures that require robust construction and precise alignment.
- Tool & Die Manufacturing: Essential for manufacturing the flat surfaces of mold bases, die components, and stamping tools, where accuracy and repeatability are fundamental to the quality of the final product.
- General Manufacturing: Used across countless applications to create keyways, slots, and precisely flat surfaces on a myriad of components for consumer goods, industrial equipment, and more.
- Prototyping and Low-Volume Production: Its versatility and efficiency make plain milling an ideal choice for rapidly creating functional prototypes and small batches of custom parts, allowing for quick design iterations and market testing.
Whether you’re looking for specialized aerospace components or high-volume industrial parts, the capabilities of plain milling, especially from a precision CNC machining company, are likely integral to achieving your manufacturing goals.
VI. What to Discuss with Your CNC Machining Service Provider
Engaging effectively with your CNC Machining Services provider is key to successful project outcomes. When discussing parts that will involve plain milling, consider these crucial points:
- Part Design Considerations: Be clear about your requirements for flatness, parallelism, and perpendicularity. These specifications directly impact machining strategy and cost. Providing detailed 2D drawings and 3D models is essential.
- Material Selection: Discuss the chosen material and its specific properties. Different materials require different cutting tools, speeds, and feeds, which influence both machining time and overall cost. Your provider can offer insights into the most cost-effective and efficient material choices for plain milling.
- Tolerance Specifications: Clearly define all critical dimensional tolerances. The tighter the tolerance, the more time and specialized tooling may be required, impacting cost. Be realistic about what is necessary versus what is merely desirable.
- Volume and Lead Time: Communicate your anticipated production volume (prototypes, low-volume, or high-volume) and required lead times. This information helps the provider plan their resources, machinery allocation, and sourcing of raw materials, especially if you’re working with a cnc machining china partner.
- Cost Drivers: Understand how factors like material cost, machining time, tooling costs, and quality control contribute to the overall price. Your provider can explain how plain milling operations specifically impact these elements.
- Quality Control and Inspection: Inquire about their quality assurance processes. How do they inspect precision CNC machining parts? What are their standards for flatness, surface finish, and dimensional accuracy? A reputable precision CNC machining company will have robust QC protocols in place.
VII. Conclusion
Plain milling, with its fundamental principles and advanced CNC integration, stands as an indispensable process in modern manufacturing. For anyone seeking CNC Machining Services, understanding its process, various types, and inherent advantages is paramount. It allows for the efficient removal of material, the creation of highly accurate flat surfaces, and the production of parts with excellent surface finishes across a vast range of materials.
By engaging in detailed discussions with your chosen precision CNC machining company, leveraging their expertise in plain milling, you can ensure that your precision CNC machining parts are produced to the highest standards, on time, and within budget. Whether your needs are met by local CNC Machining Services or through the robust capabilities of cnc machining china, an informed approach to plain milling will ultimately lead to manufacturing success.